Understanding the Art of Fasteners and Machining: Developments and Best Practices
In the realm of industrial production and design, the proficiency of bolts and machining is a keystone of making certain architectural stability, functionality, and longevity in various applications. As modern technology developments and needs for effectiveness and precision rise, remaining abreast of the newest innovations and finest practices in attachment and machining becomes crucial. From the advancement of attaching technologies to the details of choosing one of the most appropriate materials, the landscape of modern-day production is continuously developing. Join us as we explore the current innovations and dive into the nuanced globe of mastering bolts and machining, uncovering essential insights and approaches that can boost your approach to engineering solutions.
Development of Attachment Technologies
Throughout the commercial revolution and into the modern-day era, the evolution of attaching modern technologies has actually been marked by continual innovations in effectiveness and integrity. Bolts, such as screws, rivets, and bolts, play a vital role in different markets, consisting of automobile, aerospace, building and construction, and electronics. The requirement for more powerful, more sturdy, and easier-to-install fastening services has actually driven innovation in the field.
One substantial growth has actually been the shift in the direction of accuracy machining techniques to develop fasteners with higher resistances and premium efficiency. This shift has made it possible for manufacturers to generate bolts that fulfill strict quality standards and deal increased resistance to rust and tiredness.
Moreover, the introduction of innovative products, such as titanium alloys and composites, has actually transformed the capacities of fasteners. Fasteners and Machining. These materials provide extraordinary strength-to-weight proportions, making them suitable for applications where decreasing weight is vital without jeopardizing structural integrity
Advancements in Machining Methods
In the realm of industrial production, the constant development of machining approaches has paved the method for unmatched accuracy and effectiveness in the manufacturing of bolts. This accurate control makes it possible for makers to produce facility and detailed bolt layouts with simplicity.
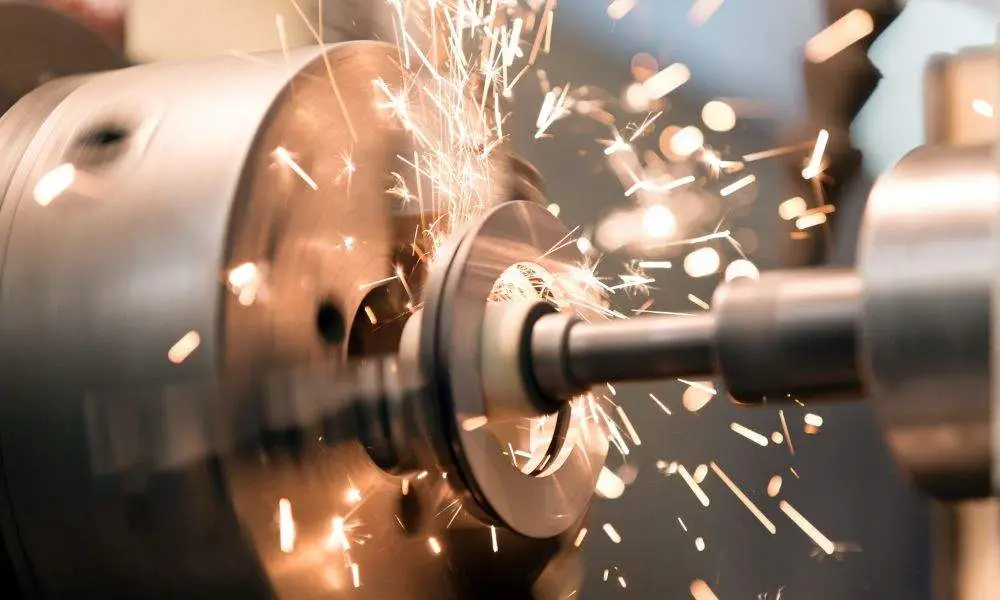
Furthermore, the adoption of multi-axis machining centers has actually enabled simultaneous reducing operations from numerous angles, even more enhancing effectiveness and lowering manufacturing times. By utilizing these innovative machining methods, makers can meet the enhancing need for top quality bolts while preserving cost-effectiveness in their operations.
Selecting the Right Bolt Materials
Picking the proper product for fasteners is an important decision that considerably impacts the efficiency and longevity of the put together elements. When choosing the ideal fastener product, several factors need to be considered to guarantee the resilience and reliability of the final item. The material picked must be suitable with the ecological conditions the bolts will be revealed to, such as temperature level variants, dampness levels, and destructive elements.
Usual products utilized for bolts include stainless steel, carbon steel, light weight aluminum, and titanium, each offering special residential properties that fit various applications. Stainless steel, for instance, is recognized for its corrosion resistance, making it perfect for aquatic or exterior atmospheres. Carbon steel is an economical choice ideal for numerous general-purpose applications. Light weight aluminum is light-weight and often used in markets where weight Going Here is an essential aspect. Titanium, on the other hand, is corrosion-resistant and incredibly solid, making it ideal for high-performance applications.
Enhancing Precision in Machining
Attaining optimum accuracy in machining is essential for making certain the quality and performance of machined parts. Precision in machining refers to the capacity to constantly create parts within limited tolerances and with high precision. To enhance precision in machining, makers utilize a variety of advanced strategies and technologies. One trick method is making use of Computer system Numerical Control (CNC) makers, which provide superior precision and repeatability compared to standard hand-operated machining methods. CNC machines are programmable and can carry out complex machining operations with very little human treatment, leading to greater precision levels.
In enhancement to CNC machining, the use of innovative cutting tools and tool owners can also dramatically boost precision. By prioritizing precision in that site machining, producers can attain premium product top quality, tighter tolerances, and improved overall efficiency of machined components.
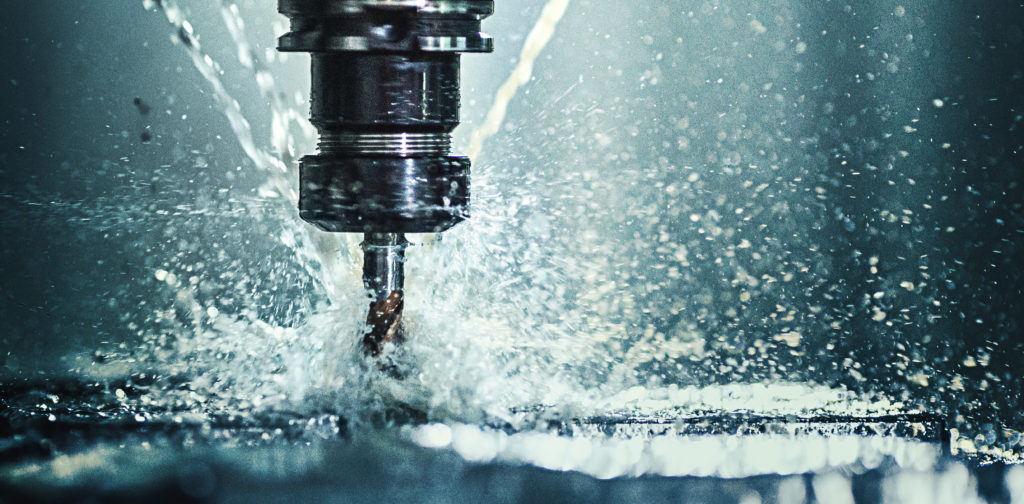
Finest Practices for Fastener Installation
Precision in machining plays an essential function in ensuring the dependability and longevity of bolt installations. When it pertains to best techniques for bolt installment, one crucial element is the correct choice of bolts based upon the particular application demands. Making use of the proper type, size, and material of fastener is necessary to assure optimal efficiency and durability. Fasteners and Machining. In addition, it is extremely important to follow maker guidelines and recommended torque values during the setup procedure to avoid over-tightening or under-tightening, which can result in premature bolt failing.
Additionally, ensuring that the bolt threads are clean and cost-free of particles before installment is vital to attaining a secure and effective connection. Making use of thread-locking compounds or washing machines can likewise boost the security of the fastener assembly. Routine assessments and upkeep of bolts post-installation are suggested to recognize any potential concerns early and prevent costly fixings or replacements in the future. By sticking to these finest practices, manufacturers can maximize the stability and efficiency of their fastener installations.
Verdict
To conclude, the evolution check here of securing technologies and improvements in machining methods have dramatically enhanced the performance and efficiency of fastener installation procedures. By choosing the appropriate bolt products and improving precision in machining, suppliers can attain ideal results in their operations. Complying with finest techniques for bolt setup is essential in ensuring the durability and dependability of settings up. In general, understanding the art of bolts and machining entails continual development and adherence to ideal practices.
In the world of industrial production, the continuous development of machining approaches has actually led the way for unprecedented precision and efficiency in the manufacturing of fasteners.Precision in machining plays a crucial duty in making certain the dependability and longevity of fastener setups. When it comes to ideal methods for bolt installation, one essential aspect is the proper option of bolts based on the certain application requirements. By choosing the appropriate fastener products and boosting precision in machining, producers can achieve optimal results in their operations. Overall, understanding the art of bolts and machining entails continuous innovation and adherence to finest techniques.